Table of Contents
Manufacturing Cost Categories, Pricing Factors, and How to Calculate
Monitoring and controlling expenses are the best ways for businesses to be both competitive and profitable. But where to begin, and what is manufacturing cost? In the world of custom parts manufacturing , your decisions hinge on a wide variety of materials, designs, and processes.
Understanding how to account for those factors is the key to ensuring your factory operates leaner and more efficiently, avoids wasted raw materials or energy, and stays resilient in the face of a weak or volatile market.
Let’s start by exploring how costs are typically calculated using some popular manufacturing cost formulas. Whether you’re involved with low-volume manufacturing or high-volume production, understanding these components will help you best control the cost of manufacturing.
The 3 Core Categories of Manufacturing Costs
Costs related to manufacturing products can typically be broken down into three categories: direct, indirect, and miscellaneous overhead.
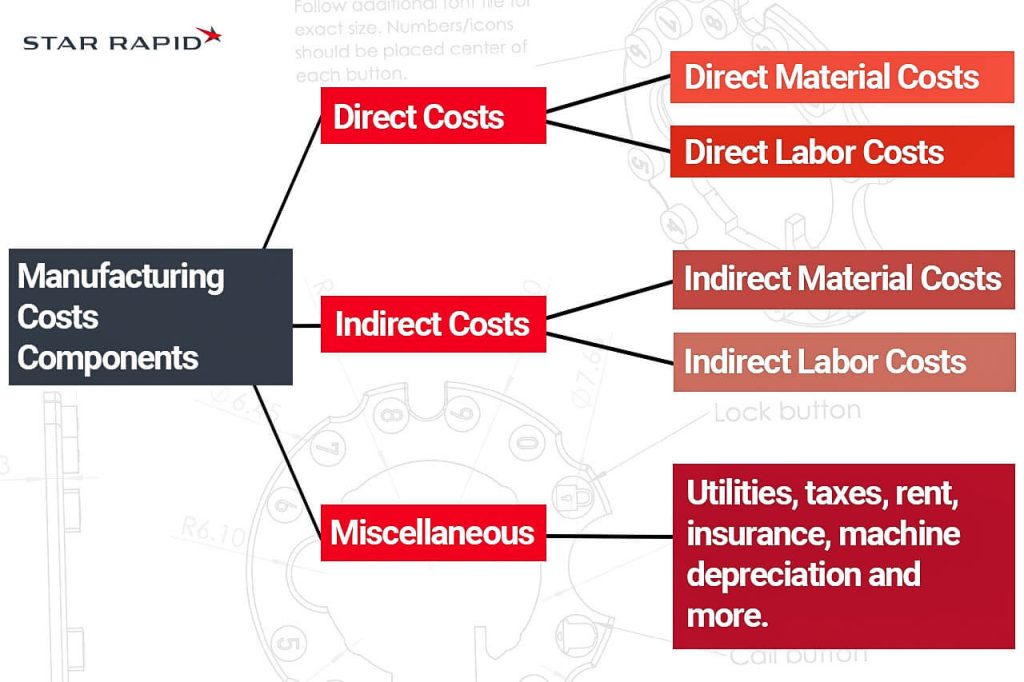
1. Direct Costs
Direct costs in manufacturing are labor and material expenses directly tied to the production of goods. These costs can be traced to a particular product or production process.
Direct Material Costs
Direct material costs include all the raw material consumed in making the finished product, including the product itself, as well as scrap, waste, or rejected parts.
Direct Labor Costs
Direct labor is the cost to the factory for employees who add value to a product or transform raw material. But make sure to distinguish the labor rate from the wage paid to the worker. The labor rate is the employee’s base pay plus overhead, which includes taxes, insurance, and benefits.
Be forewarned: It can be tricky to correctly allocate direct labor costs if the task can potentially add value to multiple products at once—like a worker who sorts and trims leather that will later be used to make many types of shoes.
2. Indirect Costs
Indirect costs—sometimes known as manufacturing overhead—are any labor and material expenses related to running a business that don’t directly add value to a product. Let’s break it down.
Indirect Labor
Indirect labor encompasses all non-production personnel, including positions like administrator, sales, marketing, or maintenance. Sometimes, a worker may represent direct labor when they’re involved in making a product, but their non-product duties, like sweeping the shop floor, would be indirect labor. The cost to manufacture isn’t tied to job titles or individuals but rather to the very nature of the service they’re getting paid for.
Indirect Materials
Materials consumed during production but not part of the finished product are classified as indirect materials. These include lubricants, abrasives, adhesives, cutting tools, dunnage, and temporary holding fixtures.
3. Overhead Costs
Manufacturing expenses that don’t neatly fit into the direct or indirect labor and materials buckets, such as utilities, taxes, rent, insurance, machine depreciation, or environmental remediation, can be accounted for in a miscellaneous category.
The Top 6 Factors Affecting Manufacturing Costs
Now that we understand how to group the components of manufacturing, let’s examine the different factors that affect the cost of manufacturing.
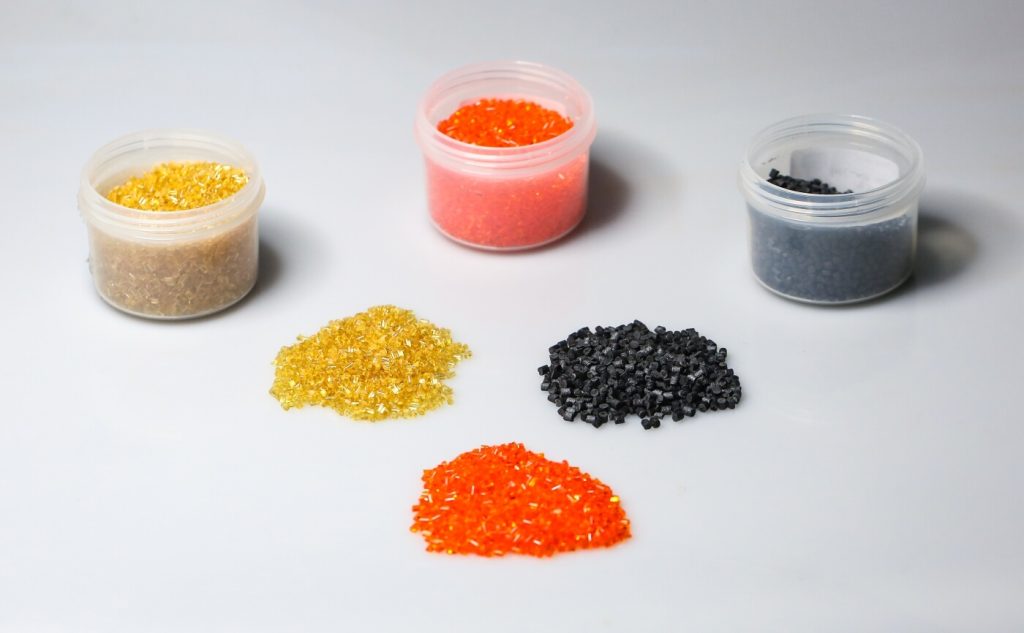
1. Labor Costs
Direct labor has a massive effect on the cost of manufacturing. The number of people involved in making a product, the time it takes to make it, and their hourly rate are expenses that managers should always seek to monitor and control.
While assessing how direct labor costs impact total manufacturing costs is fairly easy, it’s more difficult to account for indirect labor or overhead expenses.
2. Raw Materials
Raw materials are also a major cost driver. So, factory managers should attempt to conserve the consumption of raw materials. Try to:
- avoid waste
- recycle materials
- reuse materials
They can also substitute less expensive materials whenever possible without compromising product quality.
Material prices fluctuate in ways producers cannot predict or control. These fluctuations can directly affect manufacturing expenses, yet even with a secure supply of raw materials, the manufacturer is still responsible for the cost of storage, which can consume a large percentage of the factory’s valuable floor space.
Other raw materials, like food ingredients, have a limited shelf life, so they must go into production quickly or be preserved somewhere to prevent spoilage or contamination.
3. Part Complexity
Complex custom parts take longer to design, test, and measure. They typically require people with complex skills who naturally command a higher hourly pay rate.
4. Tooling
The costs of tooling, such as those used for plastic injection molding, are amortized over the entire production volume or the lifetime of the tool, whichever comes first. Since complex tools are much more expensive to design and build than simple ones, these manufacturing expenses can only be justified when making parts that absolutely demand it.
5. Volume
The general rule of thumb is that as production volume increases, the cost-per-piece decreases. This is true for stable and long-term production, where all the processes have been optimized for maximum efficiency and cost savings.
6. Precision
The term “precision” means the ability to achieve an accurate result repeatedly, so very critical tolerances can pose a threat to repeatability. There are two ways that overly accurate and tight tolerance manufacturing can adversely affect the cost to manufacture.
- First, tight tolerance features are much more expensive to make consistently, as they push the equipment to the limit of its performance envelope.
- Second, multiple critical dimensions on a single part run the risk of ‘tolerance stacking.’ Each non-critical dimension exponentially increases the percentage likelihood of making a part that’s out of specification. That’s when the scrap rate goes up, and so does the expense.
A Guide to Manufacturing Cost Formulas
Every manager should adjust the cost of manufacturing calculations based on the unique requirements of their service and the industries they serve. The general cost calculators below can be modified to suit specific applications.
How to Find Total Manufacturing Cost
The total manufacturing cost formula is basically the sum of direct and indirect material costs, labor costs, and miscellaneous expenses. Let’s find out how to account for each of these separately.
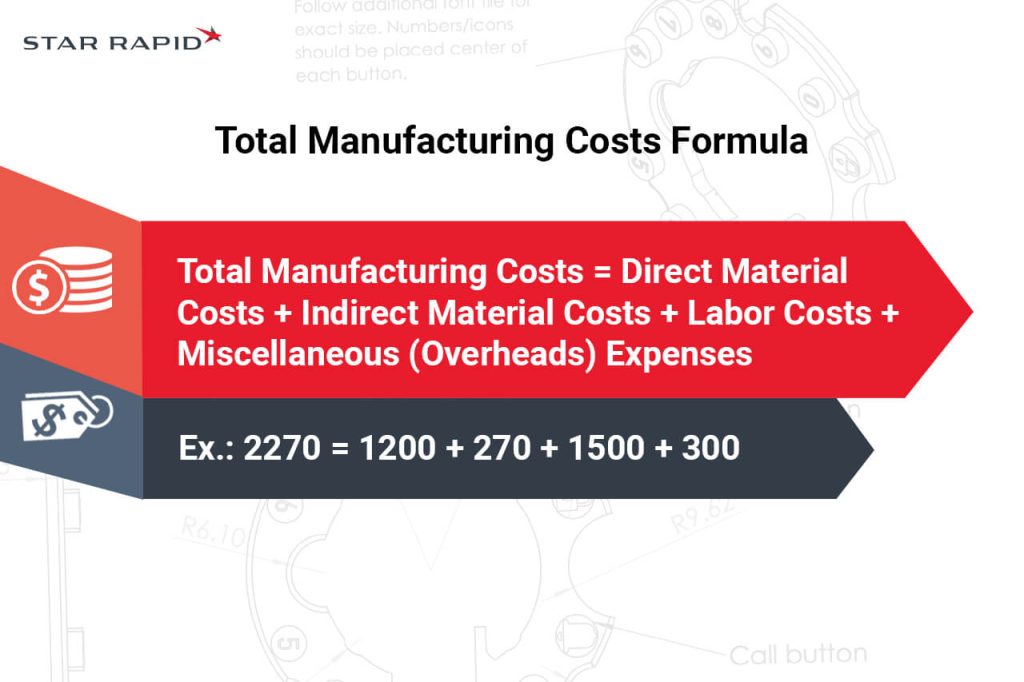
How to Calculate Direct Material Costs
Since direct materials are consumed when making a finished product, two points must be remembered to arrive at an accurate figure for this expense.
- First, remember that the purchase price for the same material can vary over time. That means that two or more lots of stock raw materials might represent two different costs depending on what they originally cost. Use that original cost in your calculation, not the current market value.
- Second, remember that raw materials that become waste during production—and hence have no value—might be useful for another product. If they do, they may regain value and wouldn’t count as lost material.
Direct Material Pre-Production Value – Remaining Post-Production Value
= Direct Material Cost
How to Calculate Direct Labor Costs
To calculate direct labor costs, add up the total number of billable hours worked by everyone performing a value-added task and multiply that time by the hourly rate. For fractions of an hour, it’s standard practice to round up to the next quarter-hour period.
Number of Production Workers x Hourly Labor Cost per Worker = Direct Labor Costs
The sum of the direct materials costs and the direct labor costs is the direct manufacturing cost—also known as the cost of goods sold. Direct costs are typically the most straightforward to quantify when calculating the cost of manufacturing.
Direct Materials + Direct Labor = Direct Manufacturing Cost
The example below shows the costs for a carpenter to produce a bespoke, high-value item for a client.
Unit | Factor | Value |
---|---|---|
A | Value of inventory pre-production cycle | $1,000 |
B | Value of inventory bought | $2,000 |
C | Final balance of inventory | $1,800 |
D | Total direct materials cost (A + B - C) | $1,200 |
E | Hours worked | 30 |
F | Hourly rate | $50 |
G | Total direct labor cost (E x F) | $1,500 |
H | Total direct manufacturing cost (D + G) | $2,700 |
Even though they’ll require additional materials for production beyond those already in the carpenter’s inventory, they will retain some of those materials after the product is finished. So, not all the value of acquired materials is lost.
However, this example shows the complexities of calculating inventory value. Though the carpenter’s remaining inventory may be valued at $1,800 per cubic inch of material, the remaining pieces of materials they purchased could be oddly shaped or too small to be used in a future project.
Producers must take a nuanced approach when evaluating inventory to make accurate calculations. Formulaic calculations are great, but they don’t always account for leftover “unusable” raw materials, leading to an unrealistic picture of the overall costs of manufacturing.
How to Calculate Indirect Manufacturing Costs
Indirect costs are the sum of indirect labor, indirect materials, and miscellaneous inputs, so let’s look at how those are calculated.
Indirect Labor + Indirect Materials + Misc. Input = Indirect Manufacturing Cost
Indirect Labor
Most businesses have a fixed monthly employee payroll, but this expense doesn’t include subcontractors, consultants, or temporary workers.
Monthly Payroll – Direct Labor Costs = Indirect Labor Costs
Let’s consider the same carpenter as before. Their indirect costs may look something like this:
Factor | Value |
---|---|
Delivering product to customer | $25 |
Workshop electricity bill | $15 |
Batteries for handheld tools | $10 |
Tool maintenance | $10 |
Total | $60 |
Indirect Materials
There are always some materials that get used up but don’t go into the finished product. For example, machines need oil and lubricants to operate, and workers use sandpaper and grinding wheels to shape and polish parts, etc. And, of course, people also need cleaning products, paper, ink, and coffee—it’s not for production, but it must be tallied. In many factories, these stock materials are kept in a physical location different from other inventory, which makes it easier to control and account for this indirect manufacturing cost.
Value of All Raw Materials – Direct Material Costs = Indirect Material Cost
Miscellaneous Overhead
Taxes, rent, utilities, maintenance, and other operating expenses that cannot otherwise be ascribed to a finished product are all considered overhead.
Accounting for manufacturing overhead costs is comparatively easy, as these tend to be fixed costs, and manufacturing overheads typically stay the same when ramping up production.
The carpenter’s overhead costs for a one-week cycle might look like this:
Workshop rent | $100 |
Administration (at $20/hour) | $20 |
Travel to and from the workshop (cost of gas) | $30 |
Total | $150 |
The Challenges of Calculating Manufacturing Costs
Calculating the true cost of manufacturing takes a nuanced approach to certain changing factors and situational variations in production.
Communication Between Departments
Large factories with more physical separation between workers and departments pose a unique challenge when allocating resources effectively. Those gaps make it tougher to avoid waste or material order duplications, so having clear communication between departments is essential.
Production Volumes and Product Customization
It’s usually more cost-effective to buy in bulk for common raw materials that are used often, but this is a substantial investment that may not be recouped for a long time. Any raw material must also be stored and preserved in the meantime, which is often overlooked as a manufacturing expense.
Variability in Labor Input
It can be challenging to say how much time a given worker puts into added-value operations if some portion of their time is spread out over multiple products simultaneously—such as with an account manager or production shift supervisor. In cases where a clear link between labor and value can’t be established, the cost to manufacture becomes indirect. However, managers try to avoid indirect labor as much as possible since it detracts from their profits.
Accuracy of Data
Factory owners and managers must have accurate data to make smart decisions about controlling and allocating resources. Collecting this data over a long period relies on worker input, careful account management, and the implementation of modern Enterprise Resource Management (ERP) software.
Rework on Scrap
Imagine that a certain quantity of raw material works its way through a manufacturing facility, slowly being transformed into a finished product. At any stage on this journey, the semi-finished article can be rejected because of a quality defect or non-conformance.
Rejected parts are expensive for several reasons. First, they represent the waste of raw material that, in many cases, can’t be reused or reworked. Second, rejected parts also contain the cumulative added value that went into them prior to their rejection. Each subsequent step in production makes the material more valuable and, thus, more costly to replace.
Best Practices for Controlling the Costs of Manufacturing
Savvy factory managers use these strategies to control the cost of manufacturing in their facilities.
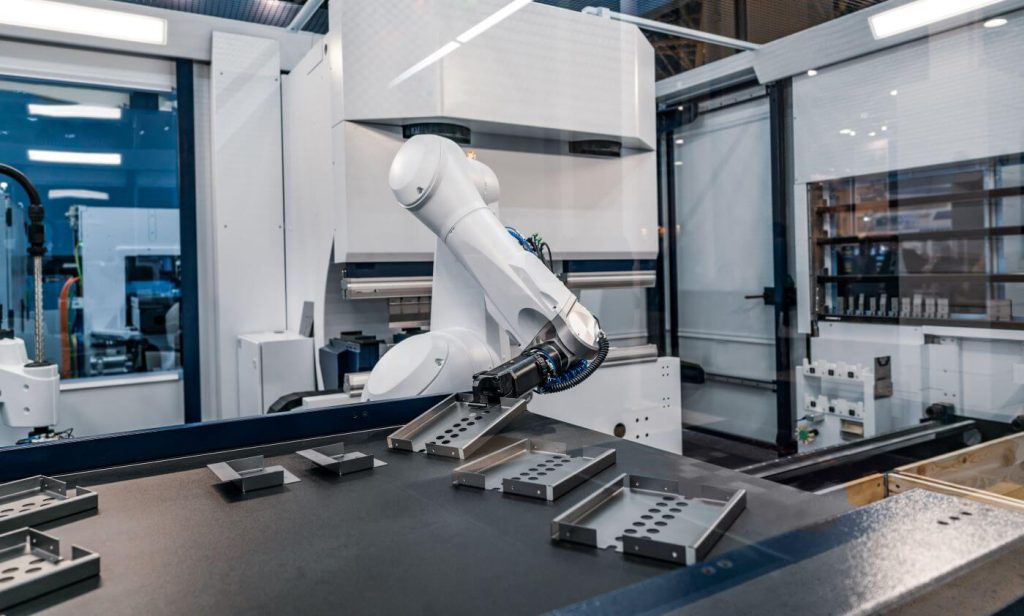
Lean Manufacturing
Customers only want to pay for what offers value—anything else is considered waste. Therefore, the purpose of lean manufacturing discipline is to reduce material consumption and waste, increase the value of all direct labor inputs, and reduce other expenses that don’t add value to the final product.
Supply Chain Optimization
A factory can only make finished parts if they have raw materials in stock when a production order arrives. At the same time, it’s costly to hold on to excess raw materials in anticipation of future orders.
Managing the supply chain effectively directly impacts the cost of manufacturing a product. That’s why working with reliable vendors with consistent delivery schedules is essential. This, combined with accurate order forecasting, ensures that the correct volume of material arrives at the factory only when needed.
Automation
Some of the best ways to control the cost of manufacturing are through machine-augmented manual work and automation of repetitive tasks. The best part of machine automation is that, unlike human labor, it provides consistent and repeatable performance without the added expense of breaks, injury, fatigue, or illness.
Cost Benchmarking
Effective manufacturers routinely benchmark the costs of their services against those of their competitors. This not only helps gauge what price the market is willing to bear but also identifies pricing trends that may indicate the need for further cost reductions or efficiency improvements in their own operations.
Review and Optimize Manufacturing Processes
If cost benchmarking identifies that production costs are higher than that of competitors, the next step is to review the manufacturing processes and find where they can be improved.
What Are the Benefits of Calculating Manufacturing Costs?
Calculating the cost of manufacturing offers profitability and performance measurement. Ultimately, it aids in financial planning and reduces financial risk.
Profitability
Businesses can improve profitability by lowering operating expenses through accurate and disciplined cost accounting and management.
Performance Measurement
Cost accounting helps a business identify opportunities to improve efficiency and reduce waste—thereby saving money and streamlining processes that lead to better performance and higher production quality.
Financial Planning
Having complete and up-to-date financial information helps managers correctly plan for future production demands. This also applies to equipment investments, facility upgrades, or other expansion efforts that must be based on a realistic assessment of current and future manufacturing expenses.
Reduction of Financial Risks
Fundamentally, the benefit of accurately calculated total manufacturing costs lies in reducing financial risk. Even if a business is profitable on paper, cash flow difficulties can sink the enterprise.
Cashflow is impacted by margin on the production process and other facets of doing business. So, correctly assessing the cost of goods sold and total manufacturing overhead allows company leaders to reduce costs, increase margin, protect cash flow, and reduce financial risk.
Key Takeaways on Manufacturing Costs
Custom part manufacturing is a demanding industry that uses a wide variety of machines, materials, and processes to provide custom component solutions. Because of the diversity of volumes and material inputs involved, it’s crucial that smart business owners carefully monitor their manufacturing costs to maintain profitability.
By applying best practices along with modern analytical tools and software, savvy managers can control the cost of manufacturing while improving many aspects of their manufacturing processes.
Learn more about key manufacturing topics with our in-depth guides on the Star Rapid Blog:
- How to Manufacture a Product
- Quality Control in Manufacturing
- Materials Used in Manufacturing
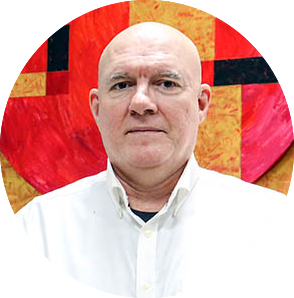
Tagged: